There is no functional or technical difference between the Item Master organization and other organizations. However, for simplicity, Oracle recommends that you limit the Item Master to just an item definition organization.
Oracle also recommends that you do not define multiple item masters. This can make item definition and maintenance confusing. In addition, multiple item masters are distinct entities, with no relationship to each other. You cannot associate items in one item master organization with another item master organization. You cannot copy items across item
master organizations.
To create the item master:
1. Use the Organization window to create the organization you want to use as the Item Master.
2. Use the Organization Parameters window to specify that organization as the Item Master. This is also where you assign child organizations to the Item Master. The item master organization uses itself as the Item Master.
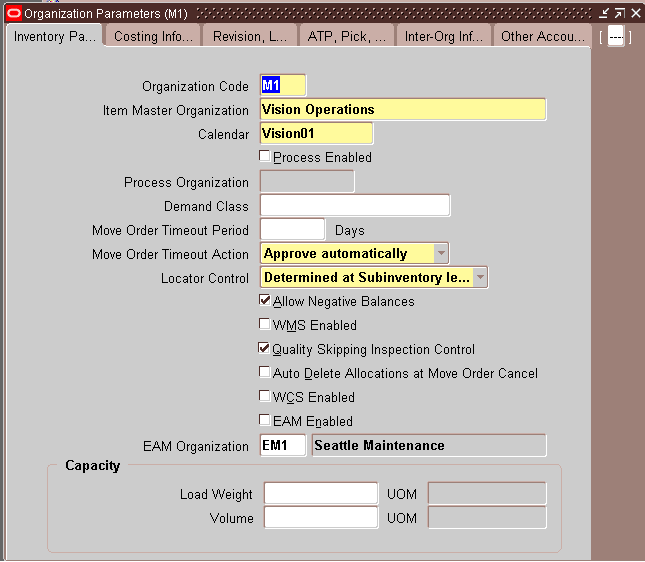
Recent Comments