- Inventory Parameters
- Costing Information
- Other Account Parameters
- Revision, Lot, Serial, LPN Parameters
- ATP, Pick, Item–Sourcing Parameters
- Defining Inter–Organization Information
- Defining Warehouse Parameters
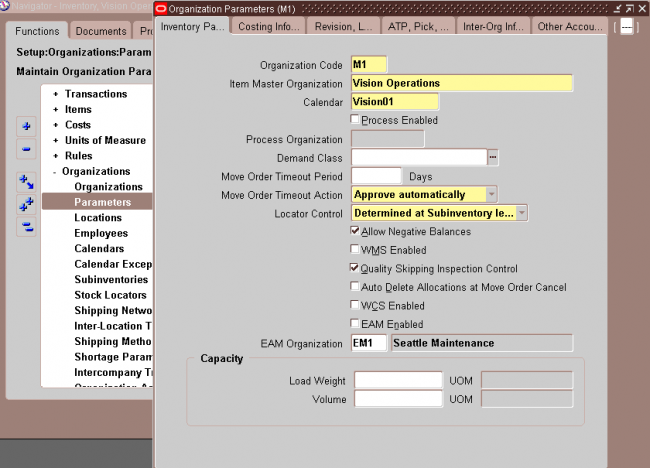
1. Enter an organization code for which you want to set up the organization parameter. 2. Select an Item Master organization. Oracle Inventory only defines items in the Item Master organization of the organization from which you enter the Items window. 3. Select a workday calendar. This is required when Oracle Master Scheduling/MRP and Oracle Supply Chain Planning is installed. 4. Optionally, select a demand class. Demand classes segregate scheduled demand and production into groups, allowing you to track and consume those groups independently. Oracle Master Scheduling/MRP and Oracle Supply Chain Planning uses this demand class during forecast consumption, and shipment and production relief. 5. In the Move Order Timeout Period field, enter the number of days a move order requisition can wait for approval. The workflow approval process sends a notification to the item planner when a move order requisition requires approval. After the first timeout period, if the recipient has not approved or rejected the order, a reminder notice is sent. After the second timeout period, the order is automatically approved or rejected, depending on whether you select Approve automatically or Reject automatically in the Move Order Timeout Action field. If you want to bypass the move order approval process and automatically approve move order requisitions, enter 0 days in the Move Order Timeout Period field and select Approve automatically in the Move Order Timeout Action field. 6. Select a move order timeout action Approve automatically: After the second timeout period, move order requisitions are automatically approved. Select this option and set the Move Order Timeout Period to 0 if you want to bypass the move order approval process and automatically approve move order requisitions. Reject automatically: After the second timeout period, move order requisitions are automatically rejected. 7. Select a locator control option: None: Inventory transactions within this organization do not require locator information. Prespecified only: Inventory transactions within this organization require a valid, predefined locator for each item. Dynamic entry allowed: Inventory transactions within this organization require a locator for each item. You can choose a valid, predefined locator, or define a locator dynamically at the time of transaction. Determined at subinventory level: Inventory transactions use locator control information that you define at the subinventory level.
- Indicate whether to allow negative balances. Determines whether inventory transactions can drive the inventory balance of an item negative.
Attention: If insufficient quantity on hand exists in a supply subinventory to satisfy backflush demand, Oracle Work in Process forces the supply subinventory balance negative, ignoring this option setting. - Auto delete allocation at Move Order cancellation
- Indicate whether this organization is an Oracle Warehouse Management enabled organization. You can use WMS features such as LPNs, task management, warehouse execution rules and cost
groups in this organization. Locator control must be enabled in order to enable WMS. Once this has been enabled and transactions have been entered in this organization, this box cannot be unchecked. - Indicate whether this organization is enabled for Quality inspection.
- Indicate whether this organization is an Oracle Enterprise Asset Management enabled Organization.
- Enter a total load weight and unit of measure for this organization.
- Enter a total volume and unit of measure for this organization.
New Features in R12
1. Select a Default On-hand Material Status tracking option. This step is optional.
Attention: You cannot update this field for existing organizations. To enable this field, you must submit the Activate Onhand Level Material Status Tracking concurrent program.
2. Indicate whether locator aliases must be unique across the organization.
Recent Comments